Our History
For more than 50 years we have developed and manufactured quality rubber products for many industrial needs.
As specialists in rubber bellows, we offer our customers an extensive standard supply program and project-specific know-how for special requirements. Choose from our wide range, our years of product experience and
an unrivaled price / performance ratio.
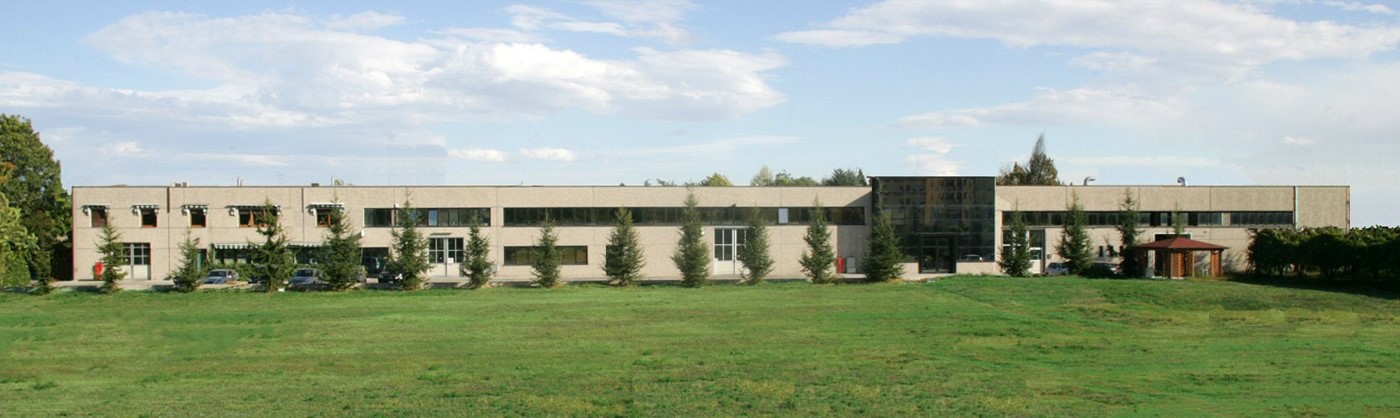
- The activity of BARBIERI RUBBER started in the year 1967, when Mr. Angelo Barbieri, after having worked at Stranieri Gomma – a company that operated in the same sector – began to produce small pieces of rubber with an old compression press in his garage at home.
- The first design produced by BARBIERI was the “leaf guard shield” in 1978. This shield is used in agricultural sprayers, replacing a similar metal plate. This patented design is affordable, secure and easily assembled.
- In 1989 the first factory was built, and the whole company relocated there, leaving the original location on Pestalozzi Street.
- In 1994 Barbieri Rubber introduced the process of injection production by purchasing from MIR the first automatic injection press with 135 ton capacity.
- In 1995 the trading company Elite Rubber, was founded, headed by Mr.Mario Neri. Under the guidance of Mr. Neri, the company’s catalog steadily grew to include shock absorbers, O-rings, seals and most significantly, rubber balls. www.elitegomma.it
- In 1999 a generational change took place. Dr. Alberto Barbieri, son of Angelo, became the CEO. Dr. Barbieri, after graduating with honors at the University of Parma and finishing a master’s degree abroad for one year, also served as technical director of robotic systems at the multinational company Elettric 80 in Reggio Emilia.
- In 2002, after many requests from customers in the field of heavy transport, the company patented a new rear buffer. ll of the components are made inside the company, using co-molding technology. The rear buffer is elegant, strong and it assembles quickly. It therefore quickly established itself in one of the most demanding sectors of the manufacturing industry.
The continuous growth of the company and its sister company Elite Rubber, necessitated the building of a second warehouse, which will be followed by a third and a quarter, expanding the company’s footprint by 6,000 meters while upgrading the company’s equipment and services with state-of-the-art technologies.
In 2005, Barbieri Rubber introduced its line of Modular bellows..
Technological advances allowed the company to produce rubber bellows in any size and prompt delivery excited the market, which in turn drove the company to realize new solutions and produce additional dimensions for their standard and modular lines.
In 2008, with the cooperation of the Austrian company Engel, Barbieri introduced the latest generation in production of rubber parts: the capillary multi-injection.
In the years 2013-2015, the company participated in a European Research study under the program: 7TH EU FRAMEWORK PROGRAM.
The objective was to produce rubber seals with a low friction coefficient and low cost. Participants included three production SME’s, including BARBIERI RUBBER, and seven European research institutes and universities.
BARBIERI RUBBER was the only Italian company to be part of the research consortium and subsequently a Royalty Free patent of the new developed technology.
TDM-SEALS FINAL PUBLISHABLE SUMMARY
In 2020, with a view to a corporate digitalization, BARBIERI RUBBER introduced the POWERMES, production management system by inserting all the production machines into the network and implementing barcode management for all other production phases.
Today the company has 35 presses with all available rubber molding technologies:
Compression, vacuum compression, transfer, injection, direct injection, injection-compression, vacuum injection, transfer injection, cold transfer injection, and multi-injection.
Our Machinery division includes:
35 injection and compression presses with 35 to 800 Ton capacity
2 mixers
1 ultrasonic washing machines
2 fridge boxes for raw materials
1 cryogenic deburring
3 ovens for post-curing
1 paint cabin for metal parts
2 sandblasting machines for metal parts